Listen to Audio Version:
Table of Contents
- The High Stakes of Medical Device Translation
- The Medtronic HVAD Case Study
- Understanding Risk Management
- Translate Throughout the Product Lifecycle
- FDA Documentation Requirements
- Quality System Regulation
- Pre-Market Documentation
- Plan for Global Distribution from the Start
- International Standards and Certifications
- Regional Classifications
- Translate Patient-Facing Documents
- Informed Consent Forms
- User Manuals and Labeling
- Post-Market Surveillance
We start with a cautionary tale.
In 2014, the Food and Drug Administration (FDA) found serious defects within Medtronics’ HeartWare Ventricular Assist Device (HVAD). Thereafter, the FDA followed standard protocol for alerting the public to substandard medical devices by taking these steps:
1. Send a warning letter to the medical device manufacturer.
2. Add the warning letter to its online database. (Making it one of nearly 3,500 current warning letters.)
3. Wait five years.
4. Clear out letters over five years old.
Boilerplate language within the warning letter states that federal agencies “may be advised” of the warning letter but only as it affects the awarding of contracts. Meanwhile, Veterans Affairs (VA) hospitals and a host of other healthcare agencies continued to implant the faulty Medtronics HVAD, leading to thousands of suspected related deaths and injuries.
Interestingly, Medtronic purchased the device from HeartWare in 2016 after the defects were well-known. This illustrates how the FDA isn’t solely at fault in these instances; both companies are arguably culpable in their complicity. In the final analysis, Medtronics only stopped distributing, selling, and using the defective product in June 2021. Currently, approximately 4,000 people worldwide are living with the device implant, with empty promises of ongoing support.
It is a heartbreaking story steeped in complexity. It illustrates how hard it is to manage known risks even in a single language framework and population (2,000 people living with the implant live in the US) in a heavily regulated industry. And that’s just one device from a database of nearly 3,500, accumulated for just the past five years. Medical devices are often distributed worldwide – comprehensive translation of information and these types of warnings mitigate risk and honor the safety and well-being of every human.
First, Do No Harm: Translate throughout the product lifecycle
The Medtronic story highlights the consequences of inadequate risk management and underscores the intricate challenges medical device manufacturers face when introducing a new product to market. Even before rollout, a product's lifecycle has at least four phases: concept, planning, design, and validation. Throughout these phases, translation facilitates clear communication between stakeholders and fulfills domestic and international regulatory requirements.
Here in the US, the FDA asks for these key documents – in English – among others, during product creation, testing, and design:
-
Device Classification: Medical devices are classified into different classes (Class I, II, or III) based on the level of risk associated with their use and determines the attendant level of regulatory requirements. Class III devices, for instance, pose the highest risk and will undergo more rigorous scrutiny.
-
Pre-Market Notification (510(k)) or Premarket Approval (PMA): Depending on the device class, manufacturers may need to submit a pre-market notification (510(k)) to demonstrate that their device is substantially equivalent to a legally marketed device or undergo premarket approval (PMA) for higher-risk devices.
-
Quality System Regulation (QSR): Manufacturers are required to establish and follow a Quality Management System (QMS) compliant with the FDA's Quality System Regulation (QSR), which addresses device manufacturing aspects such as design controls, production controls, and quality assurance.
-
Investigational Device Exemption (IDE): If a manufacturer plans to conduct clinical trials to collect safety and effectiveness data for a new device, they may need to obtain IDEs from the FDA before initiating the trials.
-
Device Specifications: Detailed technical specifications, engineering drawings, and schematics may require translation to ensure that engineers and developers worldwide understand the device's design and functionality.
-
FDA Facility Inspections: Manufacturers should be prepared for routine inspections and comply with Good Manufacturing Practice (GMP) regulations.
For medical device manufacturers outside of the US looking to market a new device here, a high-quality English translation is of utmost importance for successful passage through each development phase.
Next Circumvent Harm: Plan for global distribution from the start
Medical devices are distributed worldwide, necessitating effective communication and risk management across multiple languages. As of 2020, the US topped the list of countries exporting medical devices, close to 18% of manufactured products, with Germany (12%), the Netherlands (11%), and China (9%) not far behind. From the scientists and engineers collaborating across languages and cultures to the diverse participants in clinical research, international standards are varied and ever-evolving, adding another layer of complexity to the product lifecycle. High-quality translation emerges as a critical component in mitigating these challenges, ensuring that information about the device is accurately conveyed in each target language.
Health Canada, the European Medicines Agency (EMEA), New Zealand Medicines and Medical Devices Safety Authority (Medsafe), Singapore’s Health Sciences Authority (HSA), and the UK’s Medicines and Healthcare Products Regulatory Agency (MHRA) each serve a purpose mirroring that of the US’s FDA. Each holds a membership role in maintaining – and, when necessary, revising – International Organization for Standardization (ISO) requirements:
-
ISO 13485: A quality management system created specifically for medical devices.
-
ISO 17100: A standard exclusive to translation services, specifying the requirements for all aspects of the translation process that directly impact quality. (It’s important to note that language service providers (LSPs) do not require ISO certification; manufacturers and other stakeholders are responsible for acquiring translation services that meet ISO requirements.)
Similarly, the European Union (EU) requires instituted revised Medical Devices Regulation (MDR) requirements as of May 2021. The legislation reinforces the requirement that CE Marking be “visible, legible, and indelible” and added several additional standards, including:
-
Greater breadth of qualifying devices.
-
Broader scope of classification rules.
-
Tougher clinical evaluations.
-
An improved EUDAMED system, which follows the lifecycle of medical devices made available in the EU. EUDAMED will integrate the electronic systems of myriad stakeholders to improve outcome tracking and transparency.
-
Required use of unique device identifiers (UDIs).
-
Increased post-market surveillance.
The EU mandated even stricter documentation requirements for Class 3 In Vitro Diagnostic (IVD) medical devices one year after its revised MDR. Class 3 IVDs hold the greatest risk for patient participants during testing, and pre-and post-market performance data is continually reported on and monitored. Clinical trials are critical to IVD testing and welcome increasingly diverse populations, reflecting our current world demographic.
(Vive la Différence! High-Quality Translation Management Optimizes Qualitative Research Outcomes, QRCA Magazine, March 22, 2023)
We recently contributed an article to QRCA Magazine describing how High-Quality Translation Management Optimizes Qualitative Research Outcomes (Spring, 2023). The article centered around our translation services for a client’s medical research project, with participants from the US, UK, Germany, and Japan. Diabetic Kidney Disease (DKD) can affect a person’s whole life – the depth of patient feelings combined with the multilingual nature of the project required exacting human translation.
Patients have been seen to be less forthcoming depending on the interviewer's language or even the interview method. For example, a native Russian speaker may be less inclined to share personal feelings with a non-native speaker, and a native Japanese speaker may opt to share information only over the phone. The example poses yet another step within a product’s lifecycle requiring a translation plan. It’s important to note that in the DKD trial, AI and translation memory (TM) were ruled out as viable translation methods for any trial content.
Lastly, Always Mitigate Harm: Translate patient-facing documents with care and accuracy
“I just think they should’ve gone about it differently, told the truth, and if people still want to get it, then fine. But don’t hold back the truth. Because people have died. I was not informed about the issues, deaths, or even the recall of the pump.” -Alicia Warren, 44, from Madison, Georgia, implanted with the HVAD device in April 2018
Like Warren, many HVAD patients recall having no choice regarding the device when, in fact, another US company, Abbot Laboratories, sells the HeartMate, a left ventricular assistive device (LVAD, the general name for heart pumps) with stellar 3-year outcomes. HVAD patients talk of learning about the recall through social media, in contrast to Medtronic’s public statement claiming they had reached 90% of existing HVAD patients.
Translation and interpreting services are critical to patient empowerment when faced with such life-changing decisions. Work with a high-quality language services partner (LSP) that provides human translation and interpreting services. As stated above, in these situations, even Translation Memory (TM) can’t meet content demands. LSPs experienced in the medical and medical device manufacturing industries can easily accommodate your internal processes and Quality Management System (QMS) and uphold the highest standards of patient care, safety, and confidentiality.
Comprehensive and quality translation of patient- and physician-facing documentation facilitates an impactful product launch while complying with post-market surveillance reporting. It’s the end game, critical to the “life” in the “product lifecycle.” Pay attention to:
-
Informed Consent Forms (ICFs): Informed consent forms, protocols, and patient recruitment materials open lines of communication while promoting equity.
-
User Manuals and Labeling and Packaging Requirements: Labeling and packaging must clearly and accurately describe the device, including instructions for use (IFU), warnings, safety certifications, and precautions in a standardized format.
-
Unique Device Identifier (UDI) System: Manufacturers must assign a unique identifier to comply with the UDI system, which tracks and identifies medical devices throughout distribution and use.
-
Software and User Interface (UI) Documentation: IFUs and related documentation is essential, especially for medical devices with embedded software.
-
Training Manuals and Protocols
-
Marketing and Promotional Materials
-
Legal and Contractual Documents: Translating legal documents, including patents, contracts, licensing agreements, and intellectual property documents, is crucial for protecting the manufacturer and the device's intellectual property rights.
Post-Market Surveillance Reporting requires some explanation. Compliance has always been mandatory, yet unlike the FDA, the original EU MDR was not explicit in its requirements; the new MDR gives it broad implications, specifying that:
All activities carried out by manufacturers in cooperation with other economic operators to institute and maintain a systematic procedure to proactively collect and review experience gained from devices they place on the market, make available on the market, or put into service for the purpose of identifying any need to immediately apply any necessary corrective or preventive actions.
Medical device manufacturers can only benefit from continuously monitoring a product’s performance; proactively eliciting feedback explicitly places the burden upon the manufacturer. In this light, Medtronics’ claim that they’ve confirmed contact with every participant via snail mail is, charitably speaking, disingenuous. Ours is now a social world with varied modes of communication, and we are rarely startled by the possibilities.
It’s the “new normal,” in a sense—a world where we are called on to advocate for ourselves, especially when it comes to healthcare. Arguably, the very least medical device companies can do is translate important written information and retain interpreting services for spoken communications—it’s the single most effective way to ensure every patient has a voice, agency, and a fighting chance.
Rapport International specializes in multilingual communications, providing language translation and interpretation services that are accurate and culturally appropriate. We use the right voice and the correct terminology to avoid liability, customize services to your needs, and deliver on time and within your budget. With our 100% satisfaction guarantee, you can trust that it’s done right. Contact us today if you would like more information or to get a free quote.
Popular Posts
Popular industry news, interviews, technologies, and resources.
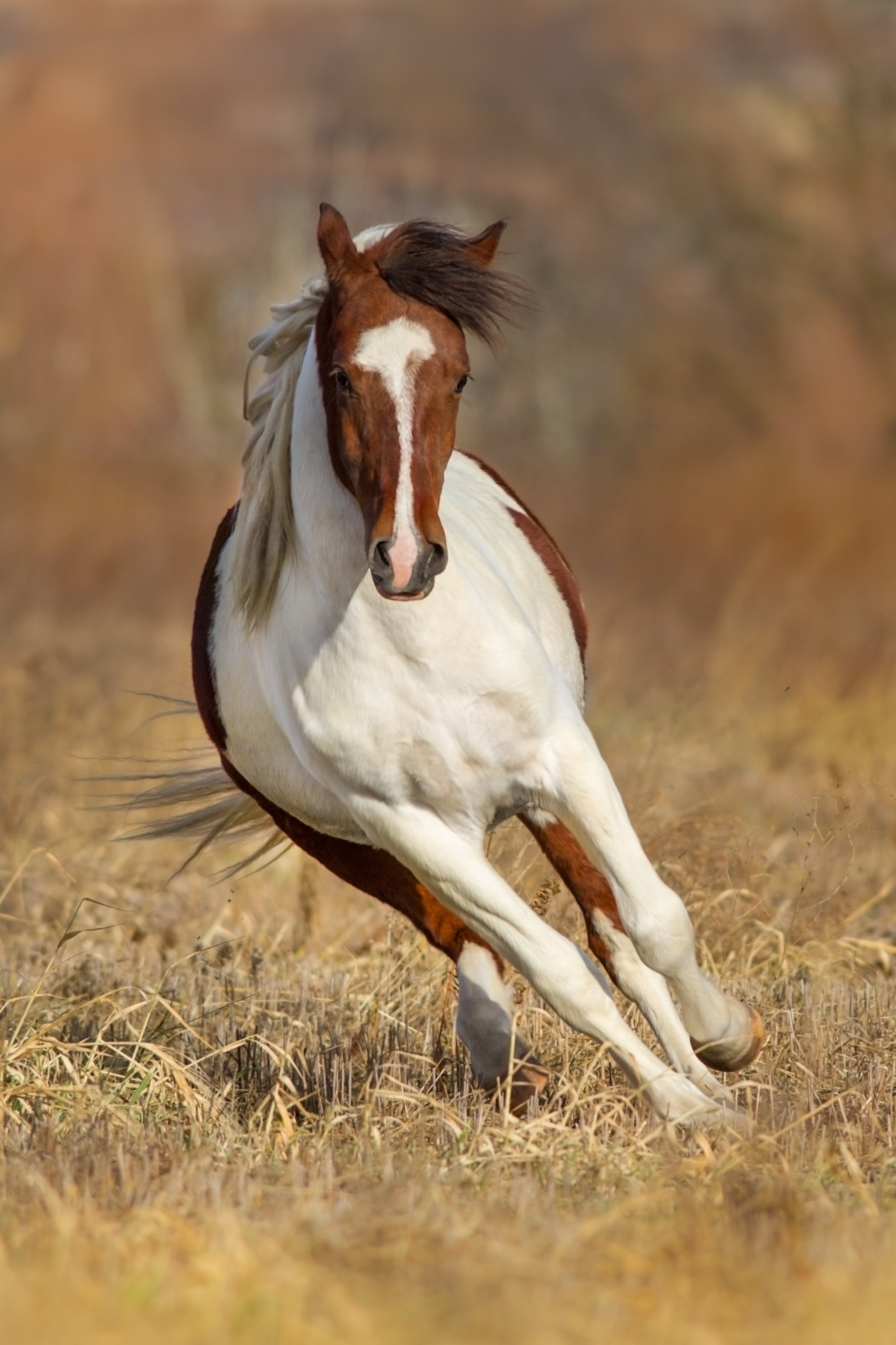
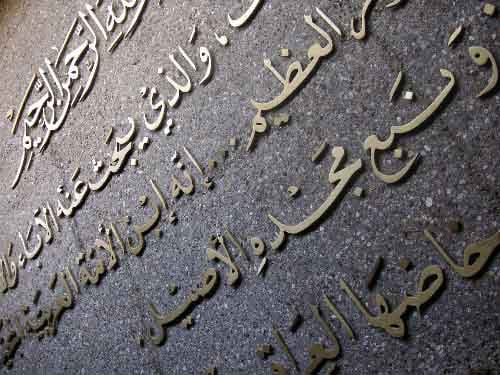
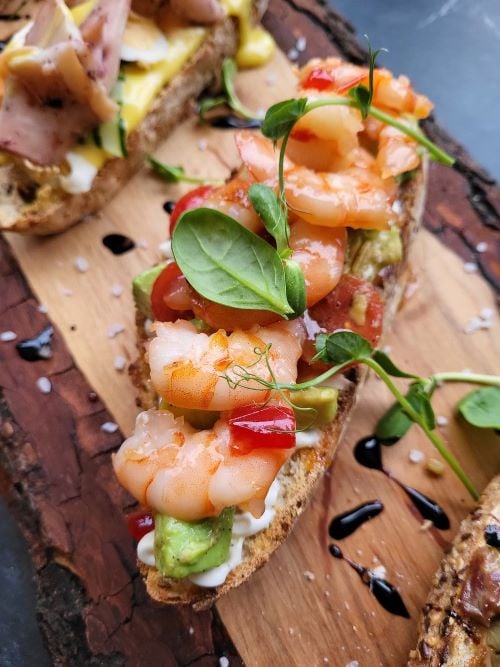
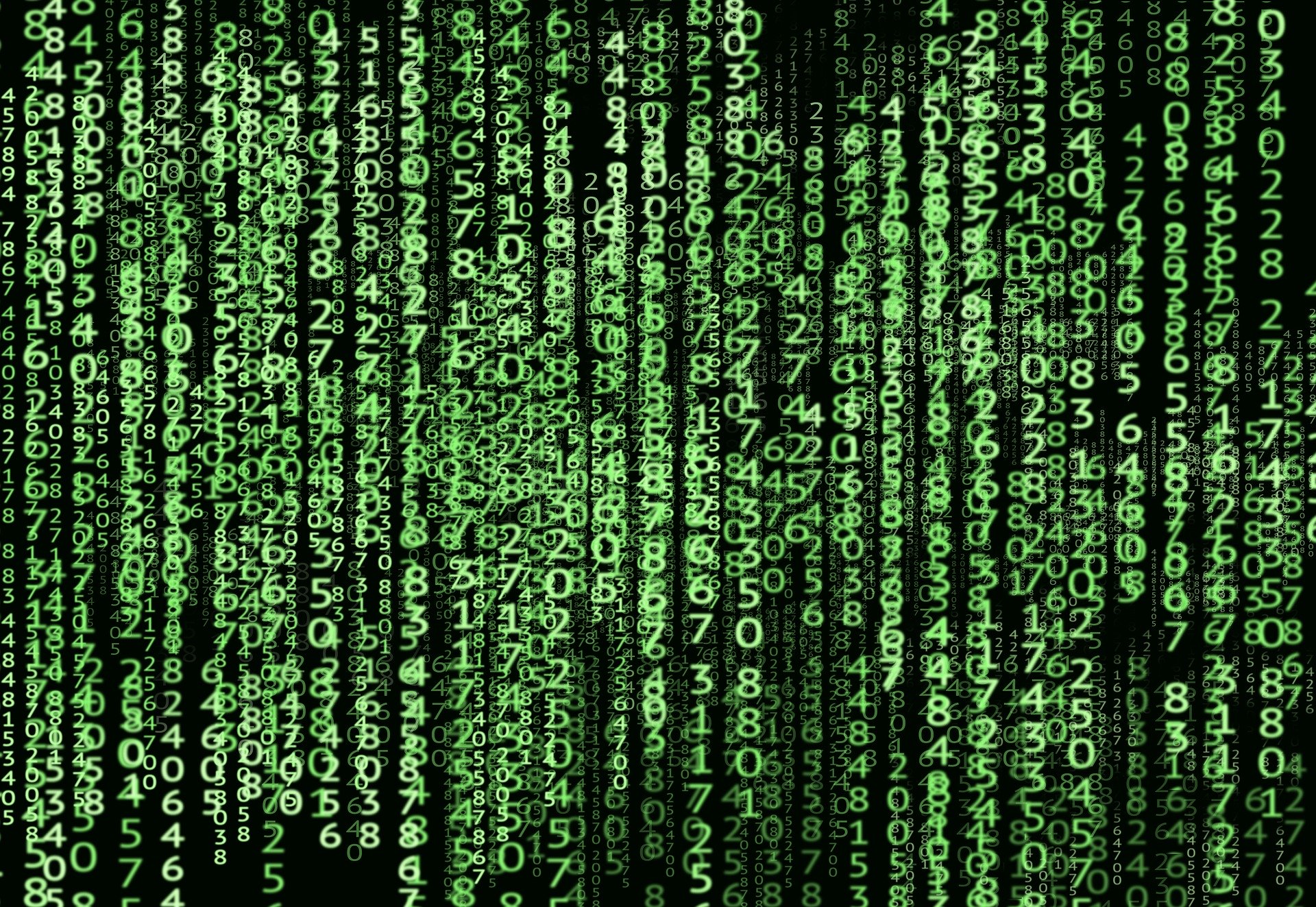
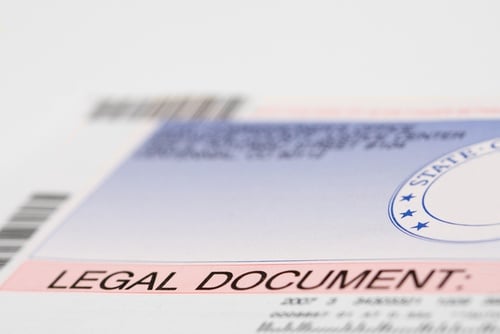
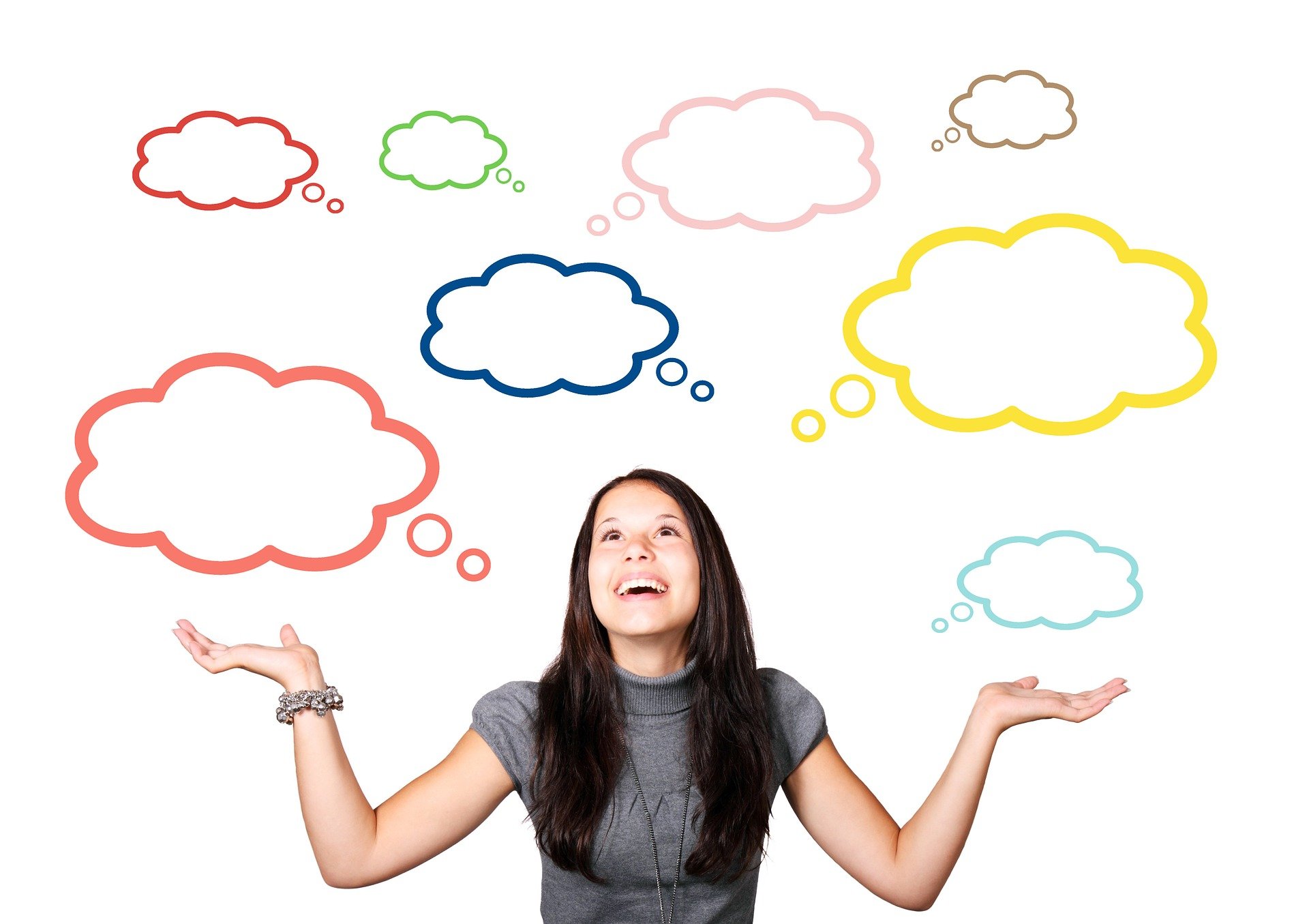
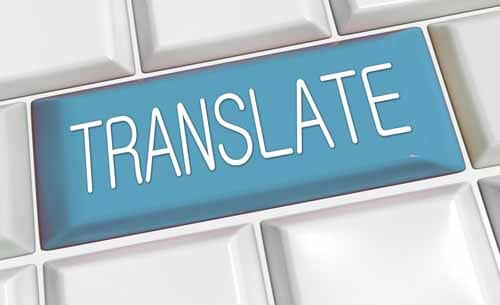
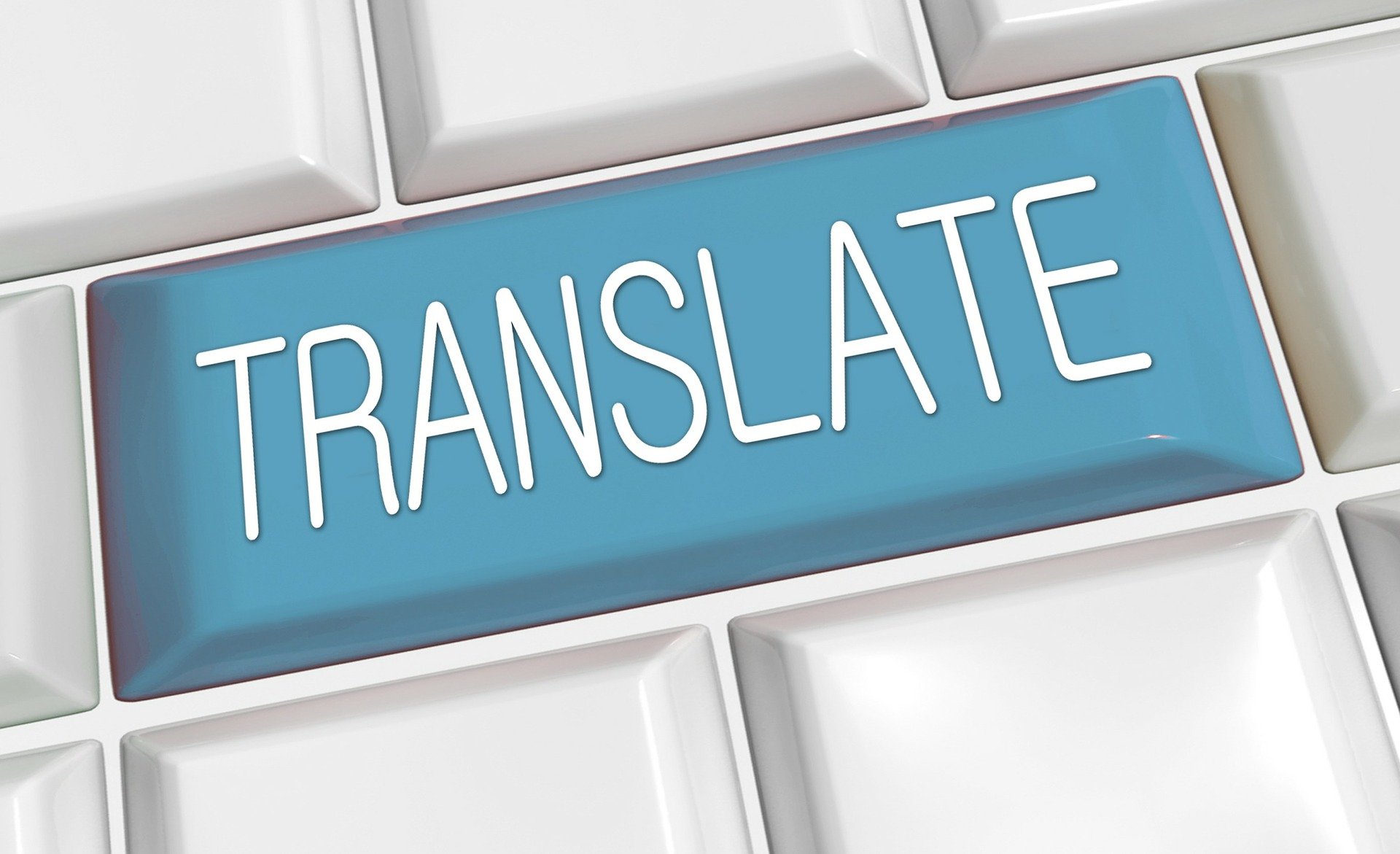
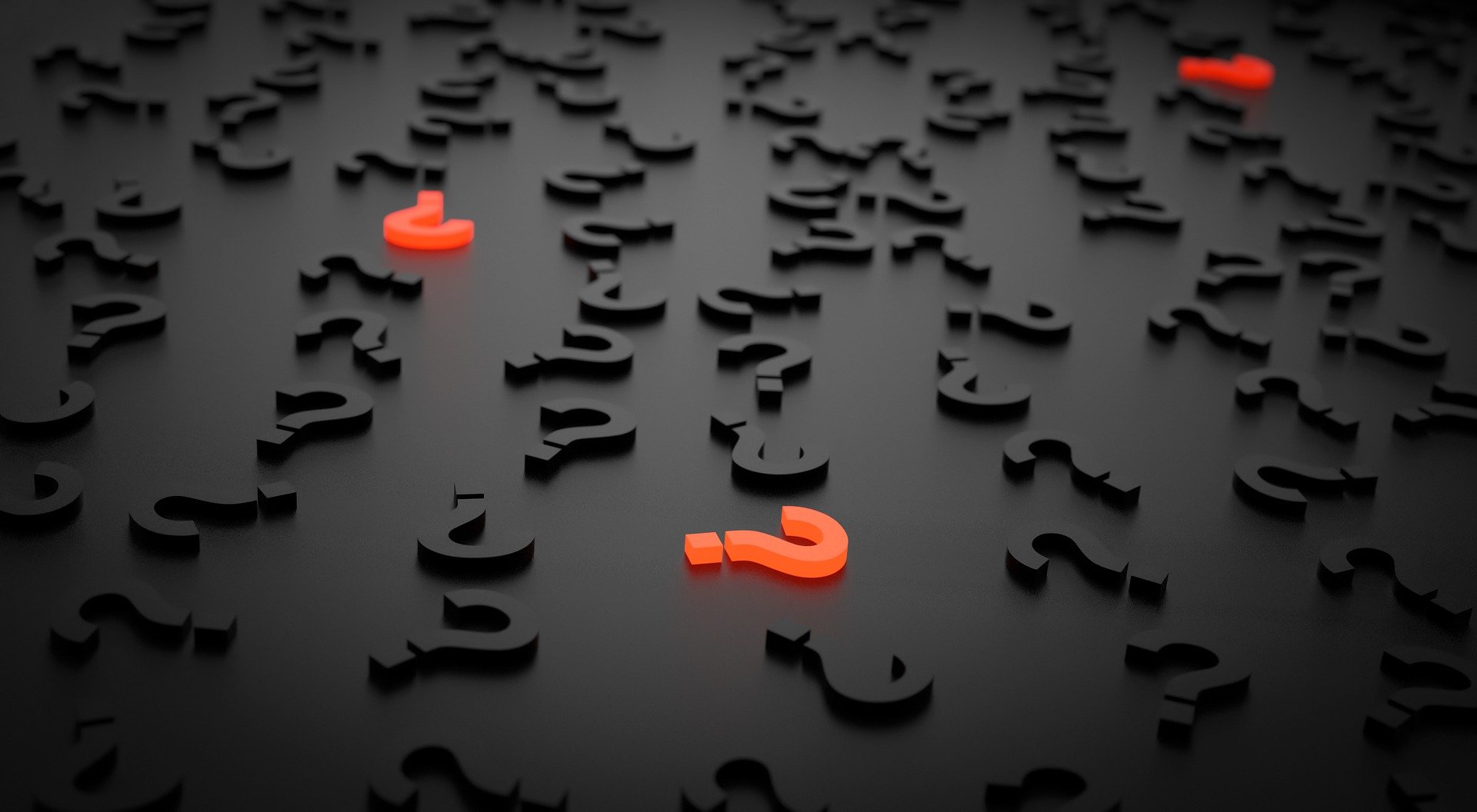
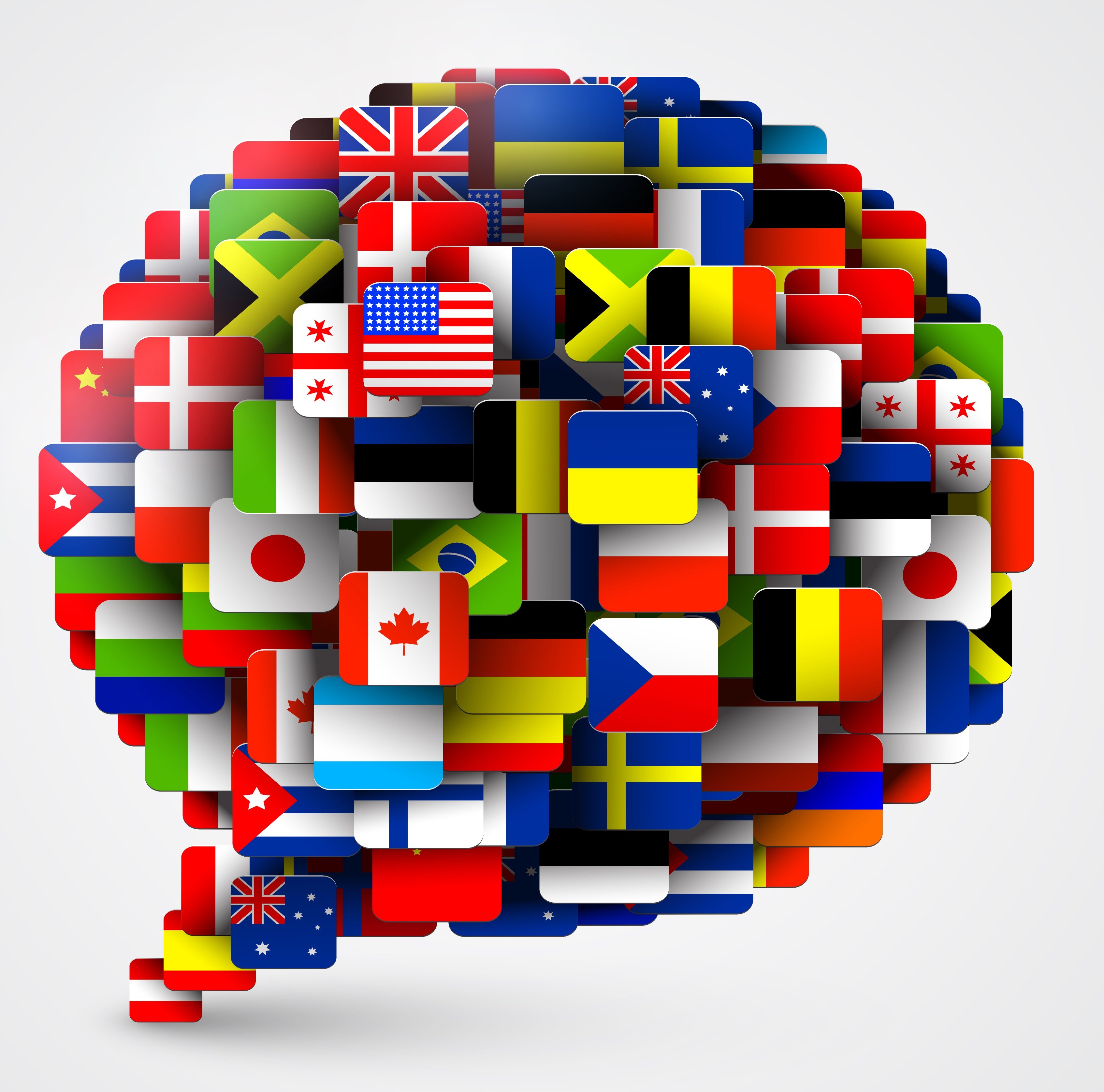